Associate Editor
- FMA
- The Fabricator
- FABTECH
- Canadian Metalworking
Tube business transformation
QTG’s new facility and equipment make tube processing more efficient
- By Lindsay Luminoso
- June 2, 2022
- Article
- Fabricating
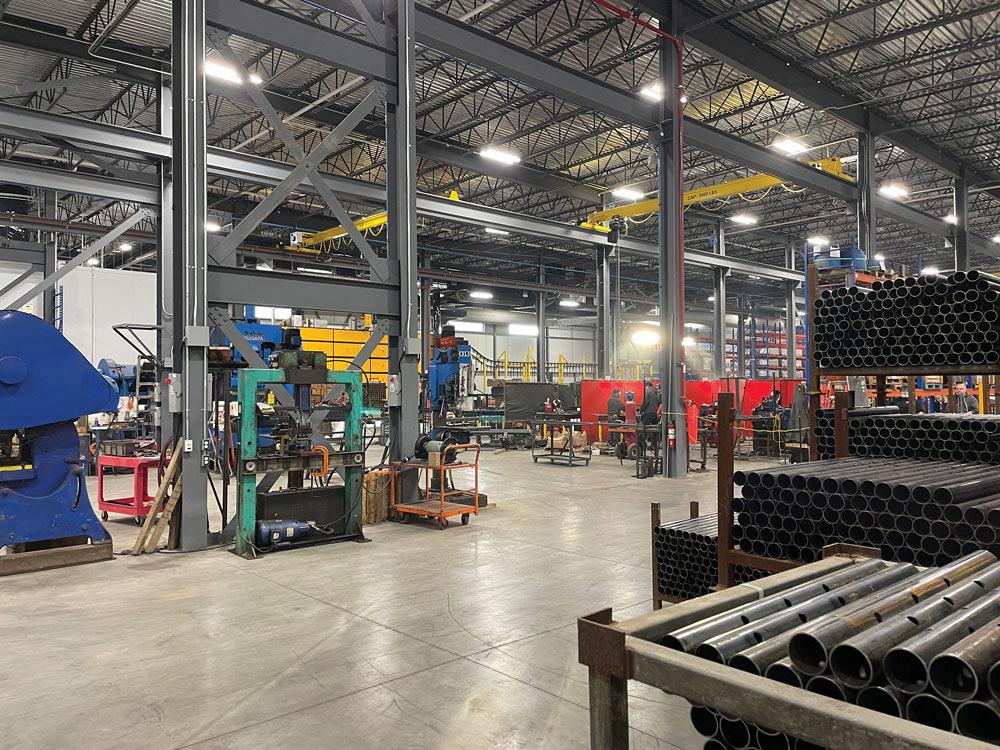
QTG recently realigned its business, expanded operations with a new facility, and invested in a significant amount of new equipment. Images: QTG
Realigning business objectives, constructing a new facility, and investing in new equipment can be stressful all on their own. But add in a global pandemic and you’ve got a recipe that could potentially break a company. That was not the case for QTG.
The Bromont, Que.-based company is first and foremost a family business. It originally started as a producer of hardware and expanded its Canadian roots to include making maple syrup buckets. Over the years the company found its footing as a galvanizer and tube manufacturer.
"We’ve been metalworkers since 1929," said Francesco Talarico, QTG vice-president. "And now we are the fourth generation of Talaricos in the business. My brother Giancarlo is the president and my father Frank is still involved as a shareholder."
In 2020 the company underwent a real shakeup with the sale of its tube mill division. Formerly known as Quali-T-Groupe, Quali-T-Tube, and Quali-T-Fab, today the company operates under the QTG banner.
"QTG is a one-stop shop for a custom, semi-custom, and OEM steel fabrication," said Talarico. "We have a core focus on the transformation of steel tubing. That’s a part of our history, and that’s the expertise that we bring to the market."
A shift occurred when the family identified an opportunity in its fabrication division, which was doing spectacularly well. As a result the company pivoted, invested heavily in value-added fabrication, and moved all operations into a newly constructed facility.
"We are seeing such incredible growth," said Talarico. "This facility didn’t exist just a year ago. I can see our old factory from my window, which is located just across the street. We moved out of a 20,000-sq.-ft. facility that didn’t really have a lot of windows on the shop floor. It was quite dark and didn’t have the space we needed to meet our production demands. Today we have a modern facility that meets our needs, and we can really grow here. We wanted to stay in Bromont because we have such a great relationship with the community and the surrounding area."
Shop Operations
The company offers a number of services including cutting, bending, punching, welding, and powder coating. And since focusing on fabricating, it has invested heavily in new equipment, specifically a new paint line, CNC laser tube cutting, and bending machines.
"We’ve equipped our shop to do just about anything, but we’re still focused on our origins in tubular steel," said Talarico. "The equipment on our shop floor was chosen to meet the needs of our existing customers and to seek new opportunities in the value-added market. Our recent investments were all targeted to help increase efficiency, safety, and a healthy work environment. We’ve made major investments in green technology, and the new factory is designed to minimize energy consumption. We wanted to minimize strenuous tasks on the shop floor through automation and ergonomics. All of these investments have had the secondary benefit of increased quality, which is critical to our customerfocused ethos."
With every investment, the company looked at new equipment through various lenses, not just production, and how it will affect the community and the environment. Strategic investments in new technology needed to help the company recycle materials and energy, limit waste, and protect air and water.
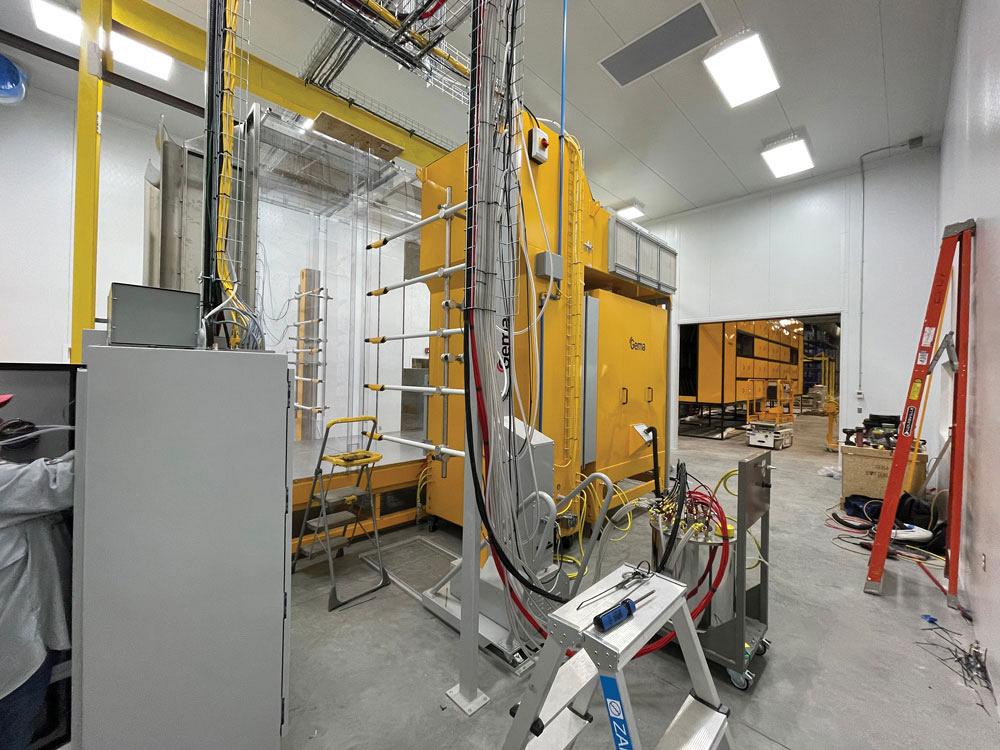
QTG’s new Gema paint system enables the company to offer higher quality finishes, durability, and aesthetic value, while the automated guns allow operators to focus on ensuring a quality process.
"Over the past year and a half we closed a division, constructed a new facility, installed about a dozen machines, produced our first order, and now we’re running at full swing speed," said Talarico. "We also implemented a new ERP system, all of this while experiencing a global pandemic. We faced a lot of challenges and not only are we here, we are growing. It’s really a credit to the perseverance of the QTG team. I also need to credit the building contractor NGA, who performed miracles for us. It’s not often that you can say a construction project comes in ahead of schedule, but that’s exactly what happened."
With a little luck and good timing, QTG was able to begin production of their support column product line before construction of the new facility was complete. Their agricultural and construction industry product lines followed shortly thereafter.
Paint Department
With an existing paint line that was more than 25 years old, the company decided it would shop around for a new paint system to enhance its shop floor.
"Our existing paint line was not a strength, but rather a packaging service we offered," said Talarico. "In the coating industry, almost anything is possible through technology. It’s critical to make the right investment and it’s easy to get carried away with all the options. That’s why we wanted to make sure we did our due diligence when shopping."
Gema Powder Coating had previously supplied the shop with its application guns, which gave QTG a sense of what to expect. Gema presented the company with a system tailored to the shop’s needs.
"Gema had the technical expertise and customer service we were looking for," said Talarico. "They designed a system that would do the bread-and-butter work we needed from it, but it would also do it with speed and efficiency. The gains in quality were incredible. This new system has elevated our ability to sell quality paint as one of our strengths."
The decision to invest in a new paint system was three-fold. First, it just made sense to upgrade equipment to suit a new facility. Second, customers had begun to demand higher quality finishes, durability, and aesthetic value. Finally, transforming their coating operations was critical to QTG’s core values: building win-win relationships, putting the customer first, and improving every day.
One of the biggest differences from the old system to the new was the switch to automated guns.
"Rather than have an operator focused on swinging his arm about 15,000 times per day, automated guns allow him to focus on quality," said Talarico. "Application is important, but all of the work that is needed to achieve and maintain that application takes place on the side of the line. Whether it’s testing chemicals, making sure the powder output is even, the gun is in the right position, or that there is good grounding, the operator needs to be available to ensure the entire process is protected. The focus now can be managing the entire line, not just the paint application. We can multiply the effect of one employee across our processes by automating wherever possible."
Training and installation were conducted during the pandemic, which presented a bit of a challenge for QTG, but the company relied heavily on Gema to help them get it right.
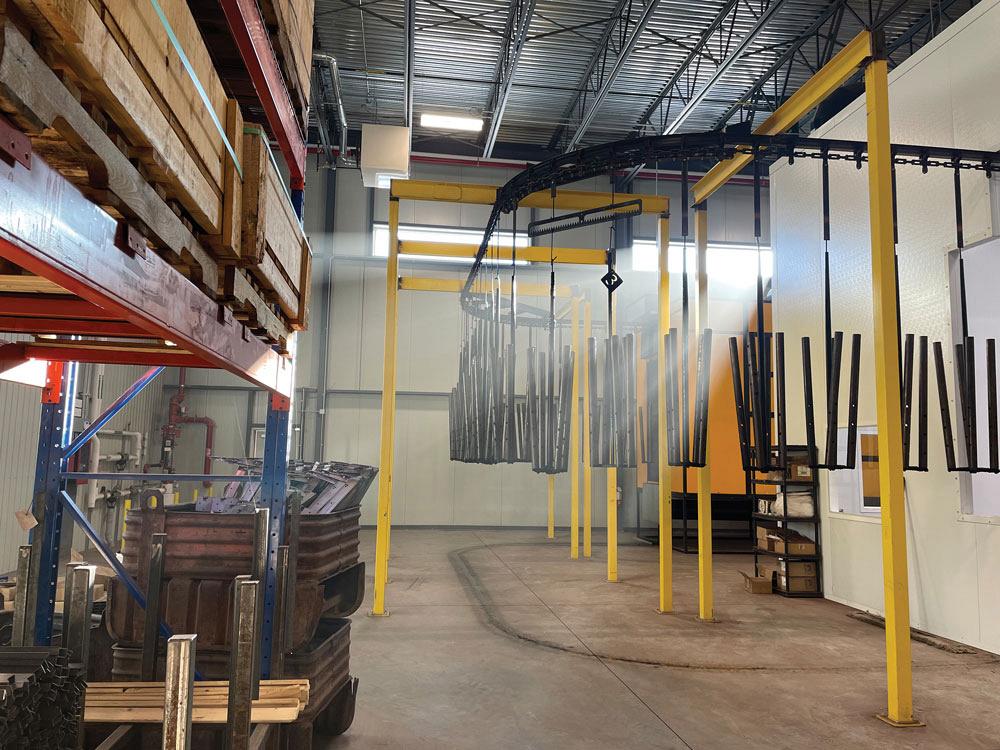
Support columns are fairly simple to paint, but projects like elevator landing gates or faraday cages can be much more difficult. However, automation has limited the challenges and the operator may only need to do a minor touch up.
"The first thing that I noticed upon installation was the simplicity of the system, and second was its robustness," said Talarico. "It’s built like a tractor, and I mean that in the best way."
One thing that Talarico likes about the system is that it has a physical switch for each control in the application process, and the interface is extremely simple. The shop’s previous system had a complicated wall of switches and blinking lights, located away from the operator’s position.
"Our operators can now walk in, pick up the equipment, and really start working," he said. "Within an hour of completing installation we were able to start the paint line up and get a good part completed on the first try."
Support columns, for the most part, are fairly simple to paint, but projects like elevator landing gates, with varying thicknesses of the steel, or faraday cages caused by expanded metal attached to the frame, can be much more difficult. Automation has reduced those challenges, requiring the operator to perform only minor touch ups when necessary. However, Talarico noted that the paint system almost always provides good, consistent results on the first pass.
"This new paint line allows us to get a quality finish the first time with less operator intervention and strain," said Talarico. "Being able to position the guns in space and move them has been revolutionary in our shop. It’s a complete transformation from two manual gun positions to 10 automated guns plus two operator positions. We’ve seen a four-fold increase in production. The quality is incomparable and our rework is almost zero at this point."
The company’s set up times have been cut in half, if not more, in some cases. The paint line also uses Gema replaceable filter cartridges, so when it needs to be replaced it’s just a matter of inputting a new one, moving from recycling to spray-to-waste much more easily and quickly.
"I also need to mention the importance of the Gema manuals," said Talarico. "The manuals often don’t get enough love from fabricators, but they are excellent and have been so helpful for us. We are able to present documentation and processes effectively and concisely. They also help with bringing new hires up to speed or help operators when dealing with challenges. They’ve really helped us grow faster."
Future Opportunities
With so much expansion and growth in such a short time, Talarico does not expect that to simply stop. QTG is exploring new product lines, new markets, and new opportunities to expand relationships with existing clients.
"We see tremendous opportunity when it comes to integrating multiple processes on the fabrication floor," he said. "Automation is absolutely the future. There’s a reason everybody talks about it, and it’s unavoidable. We also see the importance of creating an agile and expert workforce, pushing responsibility and expertise down through the organization. So my operators are the experts. It’s critical to our growth. We are just so excited for what comes next."
Associate Editor Lindsay Luminoso can be reached at lluminoso@canadianfabweld.com.
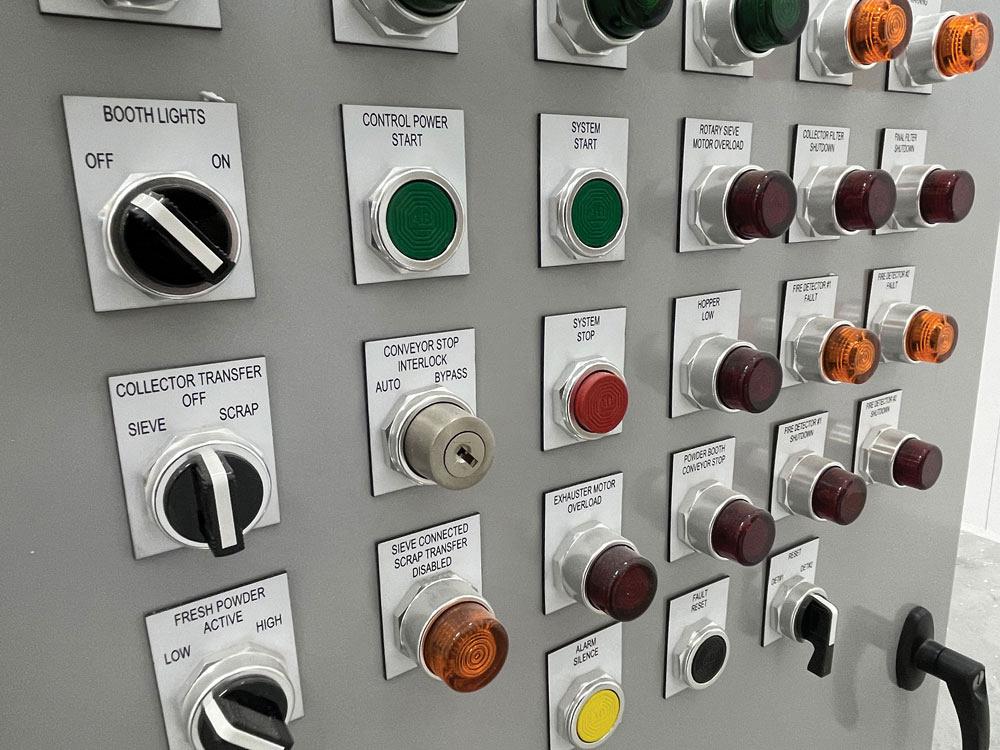
Talarico especially likes the new paint system’s control, which has a physical switch for each control in the application process and the interface is extremely simple.
QTG, qtg.ca
Gema Powder Coating, gemapowdercoating.com
About the Author
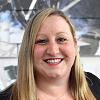
Lindsay Luminoso
1154 Warden Avenue
Toronto, M1R 0A1 Canada
Lindsay Luminoso, associate editor, contributes to both Canadian Metalworking and Canadian Fabricating & Welding. She worked as an associate editor/web editor, at Canadian Metalworking from 2014-2016 and was most recently an associate editor at Design Engineering.
Luminoso has a bachelor of arts from Carleton University, a bachelor of education from Ottawa University, and a graduate certificate in book, magazine, and digital publishing from Centennial College.
Related Companies
subscribe now
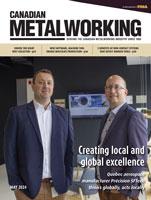
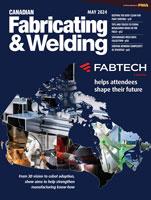
Keep up to date with the latest news, events, and technology for all things metal from our pair of monthly magazines written specifically for Canadian manufacturers!
Start Your Free Subscription- Industry Events
Automate 2024
- May 6 - 9, 2024
- Chicago, IL
ANCA Open House
- May 7 - 8, 2024
- Wixom, MI
17th annual Joint Open House
- May 8 - 9, 2024
- Oakville and Mississauga, ON Canada
MME Saskatoon
- May 28, 2024
- Saskatoon, SK Canada
CME's Health & Safety Symposium for Manufacturers
- May 29, 2024
- Mississauga, ON Canada