Associate Editor
- FMA
- The Fabricator
- FABTECH
- Canadian Metalworking
Automating quality control
Automating measuring equipment on the shop floor increases profitability, reduces cycle time
- By Lindsay Luminoso
- October 26, 2020
- Article
- Automation and Software
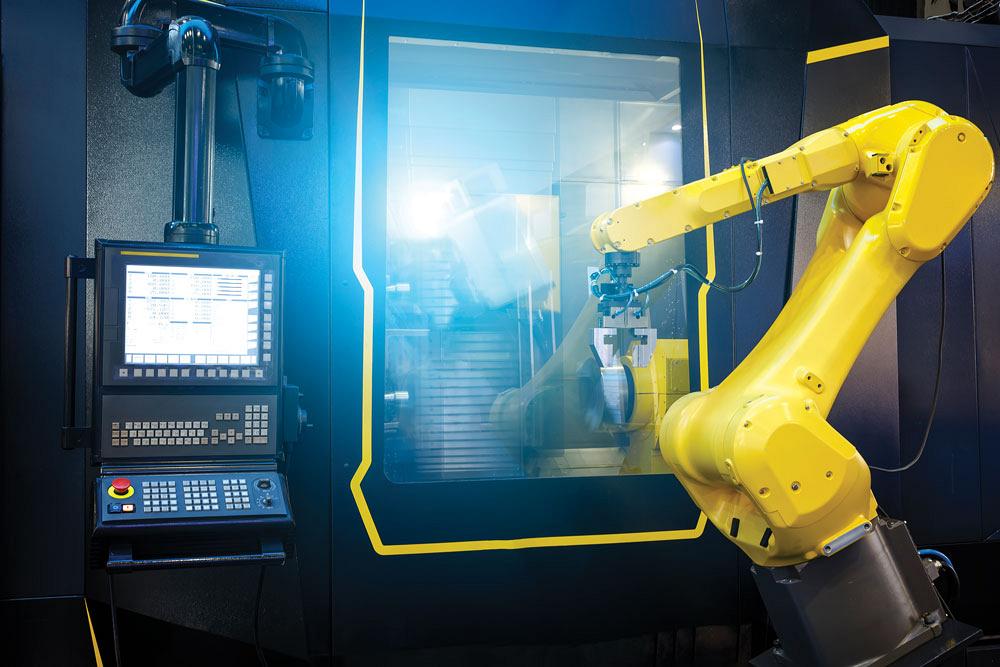
The data collected from an automated inspection system provides information about the cutting the cutting inserts, CNC machine, and more. Shops can start to see machining trends, and feedback software can step in and send an offset or adjustment to correct for errors.
The objective of most manufacturers is to produce high-quality parts as efficiently as possible. The demand for better quality and shorter cycle times continues to grow, and manufacturers are forced to adapt to meet these goals or risk lagging behind the competition.
Traditionally, quality control was either done manually on the shop floor using a dedicated gauge or the part was taken off the floor or line and moved into a controlled environment where a specialist operated a coordinate measuring machine or other metrology equipment.
Today many manufacturers are looking at how automation can work for them. However, just slapping a robot on the shop floor will not necessarily provide the production and quality gains shops are looking for. This is where measurement comes in. Adding measurement and quality control capability to an automated workcell can help shops increase profitability and gain efficiencies not only in the inspection process but in overall operations.
Cost Savings
For any shop considering automating measurement, it’s important to ensure that the investment is feasible. Especially for shops new to automation, the larger initial investment may leave them wondering if it is worth it.
"An immediate benefit is that this type of system removes the human factor in the inspection process," said David Chang, technical sales manager, Renishaw Canada, Mississauga, Ont. "Traditionally, a human operator is tasked with inspection, and with that comes the potential for inconsistency in terms of the measurement results. This is especially true when multiple operators are responsible for measurements. There is going to be that human variable and potential for error, whether it’s using slightly more force than other operators or measuring in a slightly different spot, which can make a huge difference in the results and the amount of scrapped parts. By automating the inspection process, you can increase accuracy and limit the number of parts produced out of tolerance."
The cost of the equipment ultimately depends on the type of measurement system suitable for an operation. Not all devices will be a good fit, but if a shop can demonstrate cost savings and better material usage, then the decision to add measurement and inspection into a workcell becomes that much easier.
"There is a cost to investing in such a system," said Ravi Prasad, sales and applications specialist, Mitutoyo Canada, Mississauga. "But there’s also a cost to not implementing a measurement system. And that’s by means of scrap."
Prasad gave the example of a customer who initially had a scrap rate of 5 to 6 per cent. After the customer implemented an automated system, in which machine adjustments were made based on real-time data, the shop’s scrap rate was reduced to under 2 per cent.
"It may not seem like a lot, but a 4 per cent scrap rate reduction based on a few million parts per year is huge," said Prasad. "The system easily pays for itself very quickly."
Time Reduction
Chang noted that one of the immediate benefits is removing the human factor, and from a cost savings perspective, it makes sense. But it also makes sense from a time-saving perspective.
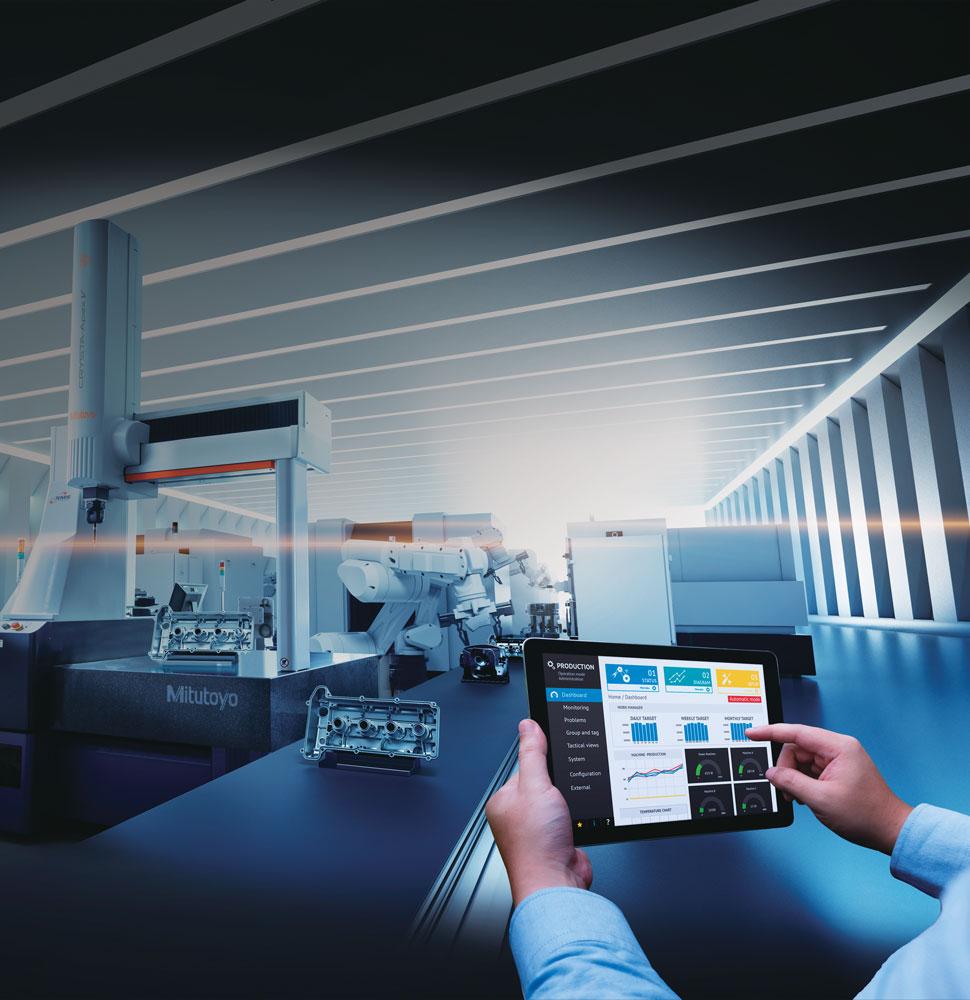
Mitutoyo’s Crysta-Apex V CNC CMM Smart Measuring System is connected to the data dashboard, which monitors the status and condition of the machine during the measurement process. Photo courtesy of Mitutoyo.
"With a manual process, the operator will have to spend the time taking all the dimensions and making sure they are correct," said Chang. "More and more we are seeing manufacturers move towards automation and inline inspection. This type of automated process can provide immediate and consistent measurement results. It’s not just making parts; it’s actually making good parts that matters."
The time it would take to scrap a part and start over is reduced significantly, and overall production times can trend downward with automated inspection.
"A benefit of integrating inspection in a workcell is that shops are able to gather information at the manufacturing source," said David Hill, commercial operations manager, Hexagon Manufacturing Intelligence, Oakville, Ont. "It removes the need to take the part off the line and journey towards the lab. That in and of itself saves time. Measuring inline or in a workcell, depending on the level of automation, can shorten cycle time. For shops with a higher rate of inspection or a high number of features to measure, automation can perform these tasks much faster than a human operator, especially now with ever-changing skillsets."
Hill added that with automated measurement there is no need for an operator to assess the part and choose the right inspection program for that particular component.
"Some of the latest automated systems can include equipment and software that automatically recognize the part or the fixture and can recall the program," he said. "This removes the need for an operator to go into the dashboard and make these decisions. So it improves the inspection and the throughput time, which is really what these systems are designed to do. It allows shops to quickly measure the right parts exactly when they need to be measured, with the confidence that it was done correctly and not requiring double-checking."
Productivity Gains
Automating measurement can be as simple as a palletized system moving parts onto a CMM or as sophisticated as an integrated automated scanner or gauging system that can capture data at a high rate. But regardless of the complexity of the system, they all offer the advantage of removing a skilled worker from the process.
"With this focus on automated inspection, shops can better utilize specialized workers," said Hill. "With the skilled labour shortage, this is significant. You are now able to use a robot or automation for basic, repetitive tasks and move operators where they are better utilized."
The operator can step back, knowing that everything will be kept within the acceptable tolerance range. "The operator can look at a report and manually make adjustments," said Prasad. "But that’s not the goal of these automated systems. What we are seeing more and more with the whole smart factory environment is that shops can use the software to monitor what’s happening with the measurement devices. Being able to gather as much information as possible, in addition to the measurement results, allows shops to be agile and react automatically on real-time data."
Chang agrees that there is a big shift in production mentality.
"Automation is more prevalent across all aspects of the shop floor, and we are now starting to see the same for inspection," he said. "When manufacturers first started to think about automation, it was more robots and conveyor systems. But as more shops move towards lights-out manufacturing and completely automating their process, inspection needs to be a part of it."
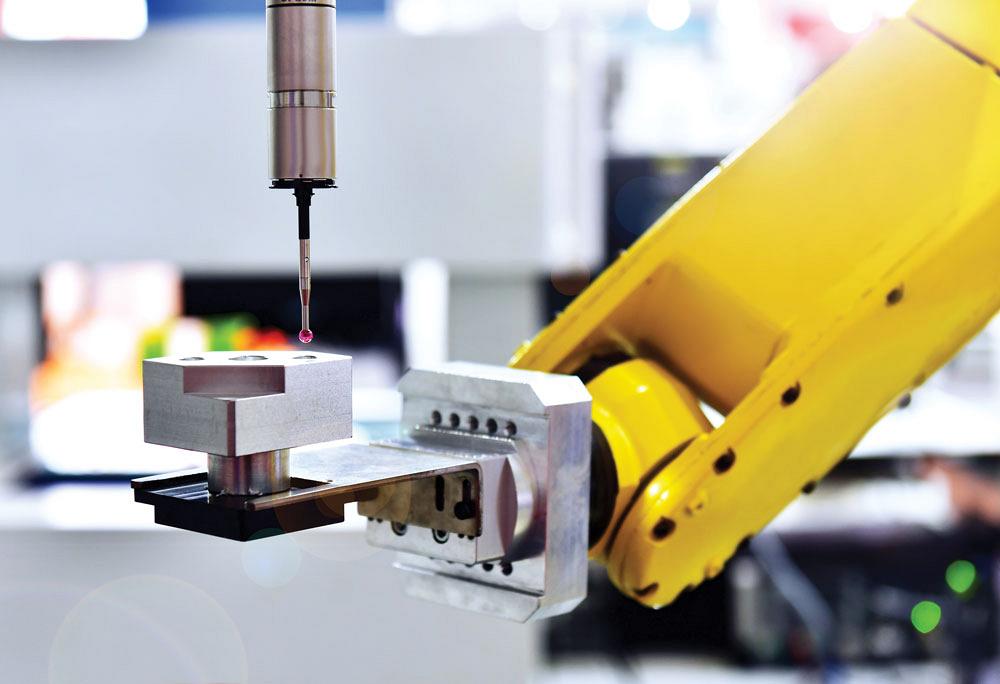
Manufacturers are increasingly moving toward automation and inline inspection, which provide immediate and consistent measurement results.
Smart factory automation as it relates to inspection is helping manufacturers learn more about the inspection process beyond whether or not parts are in spec.
"With an automated measuring system, shops can collect data," said Prasad. "But it’s when you start looking at closing the loop on the whole manufacturing process, that’s when you start seeing significant production gains, especially with feedback software. Shops can start to see trends; for example, if a tool is starting to cut a bore undersized because it is wearing, the feedback software can step in and send an offset or adjustment to correct for that."
The data collected from automated inspection provides information about the cutting inserts, CNC machine, and more. At the first instant something is off, the operator is alerted. He no longer has to wait until the part gets to the end of the line or several hours into other processes. There is no need to backtrack through processes either.
"Predictive quality is statistically driven," said Hill. "Monitoring the KPIs and controlling them within the U/L spec limits can be done via machine-to-machine communication. As the tool wears, for example, a hole will become smaller. The data will drive an offset or a tool change for that particular feature to maintain production. This information is invaluable in maintaining line rates and optimizing output."
Hill added that having a closed-loop cell capable of statistically monitoring the work flow and communicating offsets, tool wear, or breakage ensures uninterrupted production.
With automated inspection inside the workcell, manufacturers can better trust the production process.
"There tends to be a high initial investment, but the return of the investment can be easily calculated," said Chang. "Manufacturers should see cost savings as there will be less scrap; time saving as the part remains inline and data can be collected automatically; and productivity gains because the process is more consistent and can auto-adjust, making it more stable."
Associate Editor Lindsay Luminoso can be reached at lluminoso@canadianmetalworking.com.
Hexagon Manufacturing Intelligence, www.hexagonmi.com
Mitutoyo, www.mitutoyo.ca
Renishaw, www.renishaw.com
About the Author
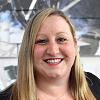
Lindsay Luminoso
1154 Warden Avenue
Toronto, M1R 0A1 Canada
Lindsay Luminoso, associate editor, contributes to both Canadian Metalworking and Canadian Fabricating & Welding. She worked as an associate editor/web editor, at Canadian Metalworking from 2014-2016 and was most recently an associate editor at Design Engineering.
Luminoso has a bachelor of arts from Carleton University, a bachelor of education from Ottawa University, and a graduate certificate in book, magazine, and digital publishing from Centennial College.
Related Companies
subscribe now
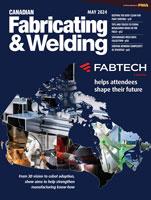
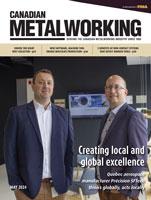
Keep up to date with the latest news, events, and technology for all things metal from our pair of monthly magazines written specifically for Canadian manufacturers!
Start Your Free Subscription- Industry Events
Automate 2024
- May 6 - 9, 2024
- Chicago, IL
ANCA Open House
- May 7 - 8, 2024
- Wixom, MI
17th annual Joint Open House
- May 8 - 9, 2024
- Oakville and Mississauga, ON Canada
MME Saskatoon
- May 28, 2024
- Saskatoon, SK Canada
CME's Health & Safety Symposium for Manufacturers
- May 29, 2024
- Mississauga, ON Canada