Technical Advisor
- FMA
- The Fabricator
- FABTECH
- Canadian Metalworking
Face milling options to leave a good surface finish
Know the role insert technology plays in creating a fine Ra
- By Andrei Petrilin
- March 21, 2022
- Article
- Cutting Tools
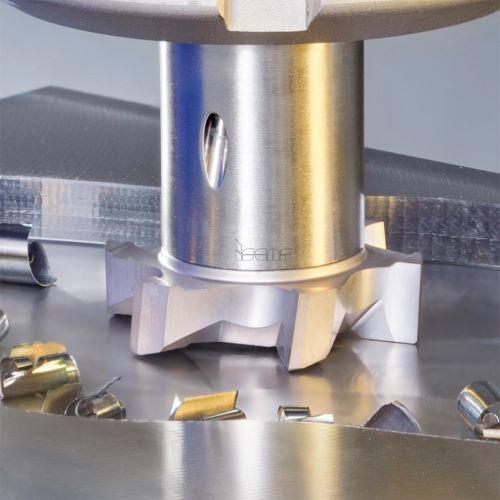
A MULTI-MASTER tool with an exchangeable face milling head made from cemented carbide can create high surface quality when milling relatively small faces, mainly bounded by shoulders. These exchangeable solid-carbide heads are available in diameters from 0.472 to 2 in.
In the metalworking industry, ensuring a high-grade surface finish is one of the main drivers of cutting tool development. This especially is true for indexable face milling cutters.
Despite seeing significant improvement in the surface quality of milled surfaces, tool designers still believe that their available resources have not yet been exhausted and that application of the latest generation of milling cutters can substantially improve surface texture even more.
Two key factors determine the quality of a generated surface: the cutter’s geometry and its accuracy. Both characteristics also are affected by the inserts that the cutter carries.
Complex Insert Geometry
Powder metallurgy processing enables the production of carbide inserts with complex shapes, which help create an optimal cutting geometry while also substantially improving accuracy. Not surprisingly, such advancements in technology have significantly improved surface finish quality when face milling.
When indexable milling cutters were successfully used to machine high-strength materials--and manufacturers started using hard milling as an alternative to grinding--the metalworking industry started demanding milling grades that created even better surface finishes in these materials.
An indexable face milling cutter is a multi-tooth tool, and more teeth equals more productivity. This is an undeniable advantage of indexable milling cutters. However, in terms of surface texture, more teeth may cause a problem. Even a small difference in tooth protrusion leads to irregular feeds for the teeth and creates chatter, which negatively affects surface finish.
Ground Inserts
Insert accuracy can be considerably increased by grinding. Moreover, grinding creates a sharp cutting edge that is very important in maintaining smooth cutting action and preventing plastic deformation of metal in a fine milling operation, which uses shallow depths of cut. Ensuring a highly accurate cutting edge requires grinding both the top and side surfaces of an insert.
This, however, may cancel the advantages of powder metallurgy in generating complicated surfaces to provide the required rake and clearance angles along a cutting edge. To avoid such an adverse effect, tool engineers should be very resourceful when designing the inserts intended for fine grinding.
An important factor regarding tooth accuracy loss is the insert’s pocket in the cutter, which has its own dimensional and form tolerances. As a result of these tolerances, even when using precise inserts, teeth protrusion varies. Of course, the variance typically lies within acceptable limits, although it cannot ensure extra-fine surface finish when compared to grinding.
A way to overcome this problem is by using a fly cutter that carries only one insert. Fly cutters facilitate a smooth and clean cut, providing excellent surface texture. But then again, their productivity is far less than multi-tooth indexable face mills’.
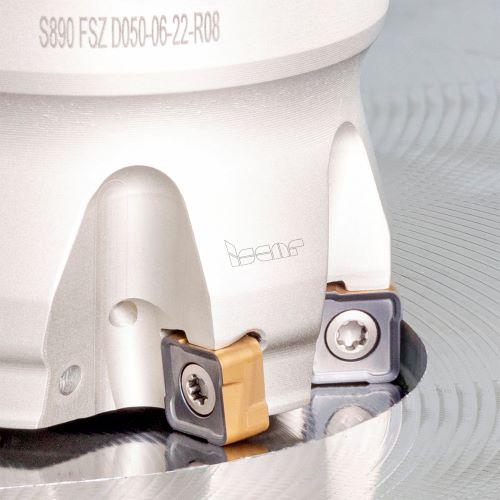
Figure 1. NEODO double-sided square rough milling inserts with an integrated wiper flat provide a good surface finish when face milling.
So how do you find an acceptable balance between surface quality and productivity? One way involves using a wiper.
An integrated wiper flat with a specially shaped minor cutting edge is a classic element of many milling inserts. Its width should be greater than the feed per revolution of the milling operation. Despite being called flat, the minor edge sometimes has a complex geometry to compensate for the negative effect of wear.
When an insert is mounted on a cutter, the wiper flat sits parallel to the machined surface. Hence, the surface will be formed by the most protruding insert of the cutter. Introducing a wiper flat in an insert design is an effective way to improve surface finish. Today even roughing milling inserts can have an integrated wiper (see Figure 1). Even double-sided inserts can have a wide wiper flat.
These tools are intended for roughing and semi-rough milling and usually require a semi-finishing operation to finish. However, some of these modern inserts can provide a surface finish up to 0.4 µm Ra when milling steel and cast iron.
Increasing the number of teeth in large-diameter face mills and fine-pitch cutters determines the width of the integrated wiper.
With these tools, a high surface finish can be achieved by using a specially designed wiper insert (or two inserts for large tools), whereby the wiper flat is significantly wider than standard. This insert is mounted in the same pocket but protrudes several hundredths of an inch axially relative to the standard insert (see Figure 2).
Great results also can be achieved by using adjustable milling cutters that have different mechanisms that adjust the position of an insert’s cutting edge within very strict limits (several microns). But the benefit of this adjustability also has a flip side. It requires thorough, fine work that takes time and patience.
Machinists don’t want to adjust a tool after mounting an insert. That is why improving accuracy using advanced geometries remains the go-to model for tooling manufacturers when they update indexable cutters for finish face milling.
New Options
Cutting tool manufacturers now offer tooling options that attract attention because of their originality. An example is a milling cutter with tangentially clamped inserts that have wide integrated wiper flats (see Figure 3).
For ensuring a high surface quality in milling relatively small faces, mainly bounded by shoulders, newly developed exchangeable solid-carbide heads are an option. The heads are fully ground and provide high precision, have a sharp cutting edge, and hold more teeth than other mills with indexable inserts of the same diameter. In combination, these features guarantee high-performance finish milling.
Andrei Petrilin is technical manager for Iscar Tools, 2100 Bristol Circle, Oakville, Ont. L6H 5R3, 905-829-9000, www.iscar.ca.
About the Author
Andrei Petrilin
2100 Bristol Circle
Oakville, L6H 5R3 Canada
905-829-9000
Related Companies
subscribe now
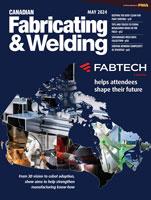
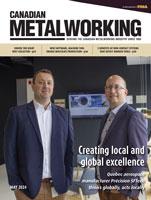
Keep up to date with the latest news, events, and technology for all things metal from our pair of monthly magazines written specifically for Canadian manufacturers!
Start Your Free Subscription- Video Showcase
- Industry Events
Automate 2024
- May 6 - 9, 2024
- Chicago, IL
ANCA Open House
- May 7 - 8, 2024
- Wixom, MI
17th annual Joint Open House
- May 8 - 9, 2024
- Oakville and Mississauga, ON Canada
MME Saskatoon
- May 28, 2024
- Saskatoon, SK Canada
CME's Health & Safety Symposium for Manufacturers
- May 29, 2024
- Mississauga, ON Canada