Technical Advisor
- FMA
- The Fabricator
- FABTECH
- Canadian Metalworking
Technology Spotlight: High-speed trochoidal tools
Advanced controls, CAM programming enable efficient, productive trochoidal milling
- By Andrei Petrilin
- August 16, 2021
- Article
- Cutting Tools
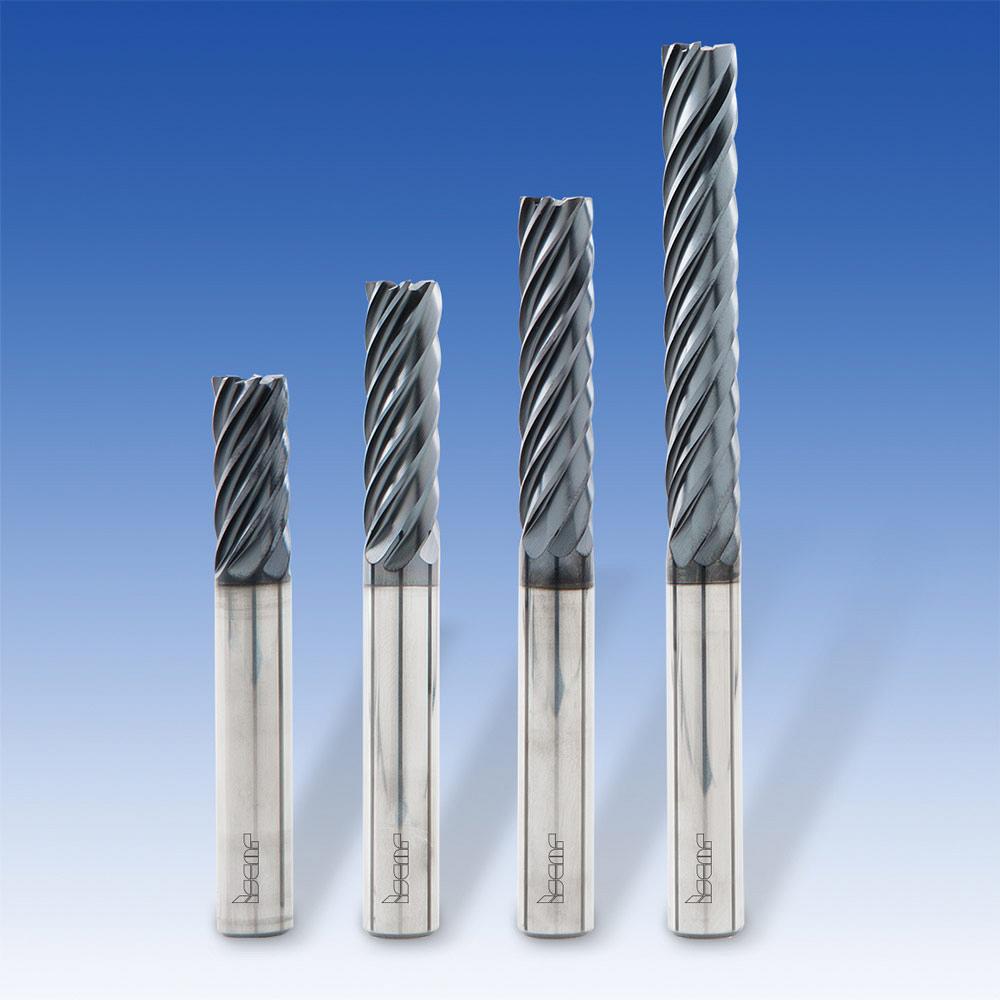
CHATTERFREE multi-flute solid-carbide end mills are available in different cutting-length-to-diameter ratios.
Several decades ago, the introduction of machine tools with significantly increased rotary and linear velocities enabled the use of efficient, high-speed machining (HSM). Peel milling, also known as slicing, was one of these HSM methods.
Peel milling couples a high DOC (usually no more than five tool diameters) with a low width of cut (typically up to 0.2 of a tool diameter). This combination offers machinists significant advantages.
Decreasing the width of cut reduces the heat load on the cutting edge and allows machinists to increase cutting speed. In peel milling, the cutting speed can be higher than in traditional milling methods. The low width of cut significantly diminishes the radial component of the cutting force, which typically causes mill bending and vibrations. Reducing this force helps ensure high operational stability and facilitates the increased DOC.
Radial chip thinning enables higher feeds to maintain the required accurate chip thickness. Therefore, milling with a small radial engagement and a substantial DOC performed at high cutting speeds and feed rates improves machining productivity. Moreover, this machining method provides gradual, uniformly distributed wear along the whole cutting edge, increasing tool life.
Productive Milling
Peel milling has proven to be productive in milling deep shoulders and wide edges. The slicing technique also is successful when rest milling, a machining process that uses small-diameter tools to cut hard-to-reach areas, such as cavity corners.
The advancement of CNC and CAM systems now has enabled even further improvement: trochoidal milling with a complicated tool trajectory instead of a linear feed motion, suitable for peel milling.
In mathematics, a trochoid is the curve, generated by the point of a circle rolling along a guide without sliding. In trochoidal milling, a cutting tool moves along a curve, slicing thin and slim material layers.
Commonly, the curve is a circular arc (semicircle) and the tool returns to the initial point by the arc chord and then repeats the path with a small stepover. In this case, the toolpath looks like the letter D. Milling along the curvilinear trajectory facilitates constant loading of a cutting edge and eliminates a sharp increase in load when the tool enters the material.
In addition to the classic D-shaped path, most advanced machines with high-end control systems can create trochoidal tool trajectories that minimize non-cutting time and optimize machine motion.
Trochoidal milling is very effective for machining deep slots, pockets, and cavities, and it is a very promising method for milling hard and difficult-to-cut materials, in particular titanium and high-temperature superalloys (HTSA). In addition, trochoidal milling is useful for improving milling performance when cutting in unstable conditions (non-rigid workpieces, thin-wall areas, poor workholding). The uniform, reduced tool loading also makes trochoidal milling efficient and applicable in micromachining.
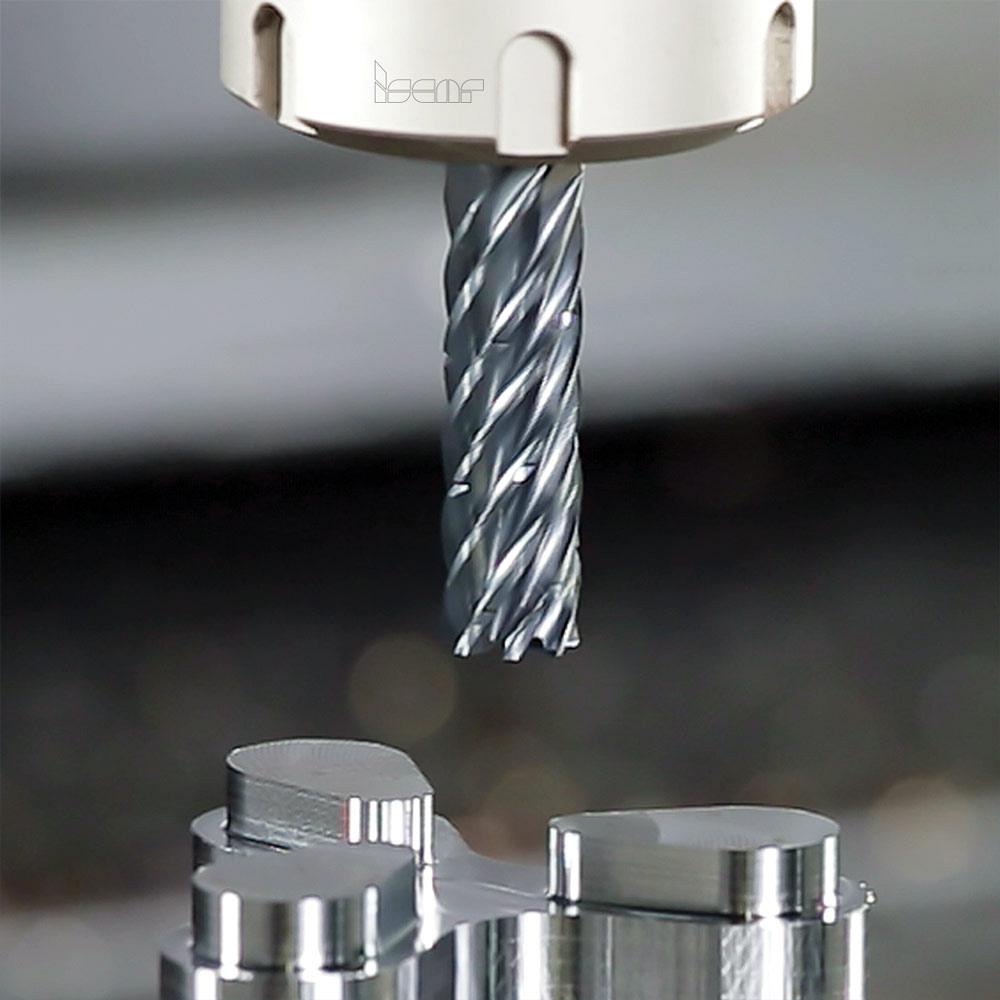
A chip-splitting cutting edge design significantly improves chip evacuation and provides satisfactory surface finish.
Trochoidal Challenges
The major hurdles in trochoidal milling are having powerful enough machine tool control and high-quality, intelligent toolpath programming. Shops also shouldn’t overlook the importance of the cutting tool. Without the right tool, all efforts to design the trajectory and maintain uniform loading on the cutting edge create poor results.
So, what are the features of a high-performance trochoidal milling cutter?
To begin with, the trochoidal milling cutter must be suitable for high-speed machining. This relates to appropriate accuracy parameters, balancing, and safety when operated at high rotational speeds.
Milling at high DOC increases the tool’s overhang, so the dynamical behaviour of the cutter is crucial to ensure machining stability. During milling with a low width of cut, only one tooth engages the workpiece material at any given time. Optimizing a contact area along the tooth is an important factor for stable milling, and using a cutter with the most favourable tool cutting edge inclination is important for finding the best fit. The effective evacuation of the thin chips, which are generated when trochoidal milling, does not require a large chip gullet in the cutter.
A multi-flute, solid-carbide end mill, or assembled mills carrying replaceable solid-carbide heads, complies with the requirements of trochoidal milling in the best way.
New Trochoidal Tools
Understandably, these end mills have their own design features, including different helix and variable angular tooth pitches that provide a vibration-resistant design to improve stability in HSM with high overhang, a specially shaped flute that results in an increased core diameter to improve dynamic strength, and enough space for the chip gullet to ensure smooth chip flow.
The diameter range of Iscar’s solid-carbide end mills for trochoidal milling is 2 to 25 mm.
CHATTERFREE EC-E7/H7-CF solid-carbide end mills have seven flutes and a variety of corner radii. They are available in a series of two, three, four, and six cutting length-to-diameter ratios (Figure 1). The end mills are produced from the PVD-coated, ultra-fine carbide grade IC902.
The key distinctive feature of the seven-flute end mill, ECP-H7-CF (Figure 2), is the chip-splitting geometry of its cutting edge. This geometry provides increased performance at high overhangs and significantly improves chip evacuation when machining deep pockets and cavities. It is important to note that the chip-splitting edge helps ensure a satisfactory surface finish for most operational requirements.
The Ti-TURBO seven- and nine-flute solid-carbide end mills (ECK-H7/9-CFR), which were designed for the high-speed machining of titanium alloys, have a cutting length of around two tool diameters. Because of their chatter dampening and an optimized edge geometry, these end mills show good results in trochoidal milling of various aircraft components, including the machining of curved slots in titanium blade rotors (blisks).
If trochoidal milling is applied to shallow slots or corners of titanium parts, the six-flute MULTI-MASTER exchangeable-head tool may be a suitable option (Figure 3). The head design enables efficient machining of hard-to-cut titanium grades such as Ti10V2Fe3Al and Ti5Al5Mo5V3Cr.
A note about toolholders, which are essential to the success of trochoidal milling, is that machining practice shows that the best results are reached when the milling cutters are mounted in hydraulic or heat-shrink chucks (Figure 4).
Andrei Petrilin is technical manager for Iscar Tools, 2100 Bristol Circle, Oakville, Ont. L6H 5R3, 905-829-9000, www.iscar.ca.
About the Author
Andrei Petrilin
2100 Bristol Circle
Oakville, L6H 5R3 Canada
905-829-9000
Related Companies
subscribe now
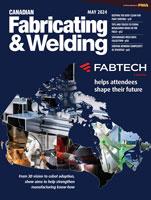
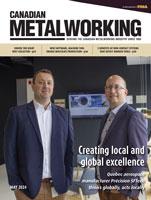
Keep up to date with the latest news, events, and technology for all things metal from our pair of monthly magazines written specifically for Canadian manufacturers!
Start Your Free Subscription- Industry Events
Automate 2024
- May 6 - 9, 2024
- Chicago, IL
ANCA Open House
- May 7 - 8, 2024
- Wixom, MI
17th annual Joint Open House
- May 8 - 9, 2024
- Oakville and Mississauga, ON Canada
MME Saskatoon
- May 28, 2024
- Saskatoon, SK Canada
CME's Health & Safety Symposium for Manufacturers
- May 29, 2024
- Mississauga, ON Canada